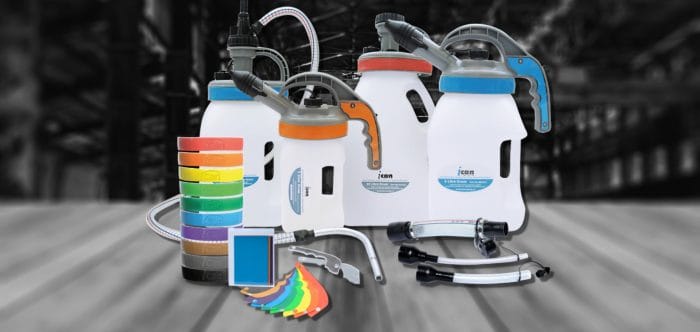
Many companies offer basic tools and equipment for fluid & lubricant handling, but most of them do not understand of what is needed.
The most common issue with viscosity problems is mixing and contamination of lubricants prior to or during the dispensing process. If this is identified to be a problem at your site, then implementing a color-coding system which visually shows the contents of lubricants will help to minimise errors.
A labelling system can be a simple concept but could prove difficult to implement and maintain.
Check with your fluid / lubrication supplier to see if they have any color coding recommendations. Often, lube color coding systems are created onsite that works, however these are often site / specific.
Color labels or markings for storage containers, dispensing points, dispensing containers and machine fill points can improve best practices, reduce cross contamination and waste of expensive fluids and lubricants.
There are several commercial solutions for labelling and color-coding fluid and lubrication systems that are very effective. You can also create your own system using excellent quality printed labels, color vinyl self-adhesive sheeting, cable ties, and color paint.
Lubricant labelling is one aspect of storage and handling that is often overlooked. Labelling is just as critical as periodic filtration and without proper labelling, it is very easy for lubricant cross-contamination to occur.
Decide how to label each corresponding lubricant from bulk storage to the equipment it will be used in.
It can be a color-coded system or an alphanumeric code system or combination of both that details important data about the lubricant, MSDS and other site specific information.
A labelling system can show what lubricant is to be used at the required location and help reduce cross-contamination. To achieve this, the labelling system must be visible, consistent and up to date with current fluids / lubricants that are in used and stored on site.
For Example, Noria’s LIS System incorporates all the best practices and does not employ product names. This allows it to remain valid even if lubricant brands are changed.
The system provides a generic specification for a particular lubricant, thus reducing the risk of machine failure caused by applying a lubricant that isn’t suited for a specific application.
A simple, highly visual or alpha numeric system that specifies the lubricants being stored in totes, drums, top up containers and the machine or equipment fill points is a key goal of a colour code and labelling system.
Correctly identifying lubricants in storage, top up containers, and their application in the field is a key component to a successful maintenance program.
Resource: Machinery Lubrication Website.